© Scriptoria
Asphalteurs - porteurs de seaux : prévention des TMS
Mis à jour le : 19/08/2025
Cette étude ergonomique porte sur l’activité des asphalteurs, en particulier les manœuvres porteurs de seaux intervenant en voirie. Ce travail physique, exposé à des risques variés (manutentions, fumées, chutes), reste peu mécanisé. L’analyse vise à mieux comprendre leurs conditions de travail et à identifier des pistes de prévention, notamment pour limiter les troubles musculosquelettiques (TMS).
Cette solution présente les principaux résultats d'une étude ergonomique* menée sur des chantiers, dans le cadre du dispositif Fipu (Fonds d'investissement dans la prévention de l'usure professionnelle) financé par la Cnam. L'étude a été complétée par les experts de la direction technique de l'OPPBTP pour identifier les situations de travail à risque de troubles musculosquelettiques (TMS) dans l'objectif de proposer des solutions pour améliorer les conditions de travail, réduire voire éliminer les TMS. Pour en savoir plus sur le dispositif Fipu, ses aides financières et les équipements subventionnés, consultez notre boîte à outils TMS/Fipu.
* cabinet Solutions Productives
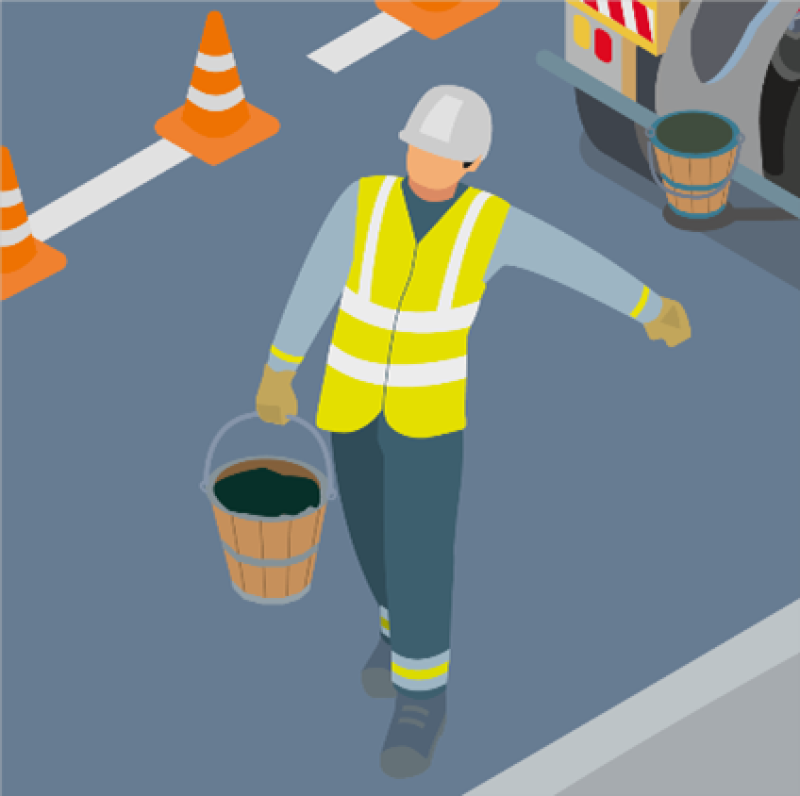
Sommaire
Principaux impacts prévention
L’activité des porteurs de seaux en voirie revêt un caractère traditionnel, et s’accompagne de contraintes physiques importantes. Certaines tâches du métier ont pu bénéficier de l’introduction de matériels innovants pour acheminer l’asphalte. Cependant, la modernisation des outils et des équipements n’a entraîné que des améliorations mineures (modifications apportées aux anses des seaux, aménagements de la plateforme d’accueil des seaux pour le remplissage…).
Pour autant, certaines pratiques professionnelles ayant un effet favorable sur la prévention sont constatées sur des chantiers. Leur généralisation comme la mise en œuvre d’actions de prévention pourront contribuer à réduire les risques de TMS pour les porteurs de seaux ; elles concernent essentiellement l’organisation du travail.
Atteintes musculaires et articulaires
En quoi consiste l’activité des porteurs de seaux d’asphalte ?
L’application d‘asphalte sur la voie publique est l’œuvre d’un collectif au sein duquel les interactions sont nombreuses, entre les porteurs, les applicateurs et le conducteur du camion malaxeur. C’est donc l’activité du porteur de seaux et celle du collectif auquel il appartient qui sont ici analysées.
L’asphalte est un produit bitumineux coulé à près de 200 °C, sans vibration. Le produit est fabriqué en usine, la nuit précédant le chantier, puis acheminé jusqu’au lieu d’application en camion malaxeur, qui chauffe l’asphalte pour le maintenir à une température garantissant sa fluidité. Il n’est pas appliqué en cas de pluie et de gel.
La diversité des chantiers est liée :
au lieu d’application, essentiellement sur l’espace public, majoritairement en voie ouverte à la circulation, mais dépend des éventuelles spécialisations des entreprises ;
à la superficie (de plusieurs chantiers de quelques mètres carrés à un chantier de plusieurs centaines de mètres carrés dans la journée) et à la nature des surfaces à recouvrir : plane ou en pente, d’épaisseur d’asphalte nécessaire variable (majoritairement 2 cm mais parfois davantage) ;
à la présence ou non d’usagers (piétons et véhicules, commerces…) ;
à l’accessibilité du chantier (distance du camion malaxeur au lieu d’application, escaliers…) ;
au type d’asphalte appliqué (majoritairement noir, de plus en plus souvent clair) ;
au cahier des charges du client : horaires, délais, motifs…
Le planning des chantiers est organisé de manière à optimiser les déplacements et le temps d’application de la totalité de l’asphalte embarqué (regroupement des petits chantiers). Malgré tout, les aléas sont nombreux : météo défavorable, accessibilité du chantier… Ils peuvent obliger à décaler les chantiers et imposer parfois des régulations de dernière minute. Même si ce type de cas reste rare, certains chantiers doivent également être réalisés de nuit.
Afin d’éviter les pertes, la quantité d’asphalte dans le malaxeur est prévue au plus près des besoins calculés pour les chantiers programmés sur la tournée. L’équipe aura pour objectif d’appliquer tout l’asphalte contenu dans le camion pour la journée, sur un ou plusieurs sites, quitte à « finir la cuve » en ne traitant qu’une partie d’un chantier, qui pourra être repris un jour suivant.
Certaines photos peuvent montrer des écarts aux règles habituelles de sécurité : elles reflètent la réalité des chantiers observés. Leur but n’est pas de montrer un exemple parfait, mais de représenter des situations réelles sur le terrain.
Un cycle répétitif jusqu'à la fin du chantier
L’équipe est choisie selon les compétences de ses opérateurs et de leur disponibilité. Le recours à l’intérim n’est pas rare.
Une équipe est composée, a minima, d’un conducteur du camion malaxeur, d’un applicateur et d’un ou plus souvent de deux porteurs de seaux. Néanmoins, l’effectif de chaque équipe varie en fonction de la surface à recouvrir et de l’accessibilité du lieu d’application ; si celui-ci est éloigné du loco-malaxeur, cela nécessitera de renforcer le nombre de porteurs de seaux.
Avant de commencer l’application, ou au fur et à mesure de l’avancement pour les surfaces étendues, l’équipe, guidée par le conducteur du camion balise la zone pour les piétons et les véhicules (cônes et panneaux de signalisation, rubalise…) et nettoie le support. C’est l’applicateur, en lien avec son encadrement à distance, qui décide de commencer l’application une fois sur place.
L’asphalte est versé dans des seaux en bois à l’arrière du camion. Les porteurs de seaux emportent ceux-ci (en général un à la fois, parfois deux) à pied d’œuvre et déposent l’asphalte à l’endroit précis souhaité par l’applicateur. Les manutentions sont effectuées rapidement pour éviter la baisse de la température du produit, garantissant la facilité d’application et la qualité finale du revêtement.
Un approvisionnement en continu s’organise pour alimenter le(s) applicateur(s) de manière permanente et régulière. L’activité des porteurs de seaux s’inscrit donc dans une succession d’actions, en un cycle qui va se répéter jusqu’à la fin du chantier ou épuisement de l’asphalte dans le camion malaxeur. Le nombre de cycles réalisés dans la journée dépend donc du nombre de porteurs de seaux et du volume d’asphalte disponible dans le camion.
Si nécessaire, les porteurs de seaux peuvent aussi asperger d’eau l’asphalte appliqué pour le refroidir et participer aux autres tâches, en aidant l’applicateur dans le calepinage, ou le chauffeur dans le balisage et l’orientation des usagers de la voirie…
On voit également une polyvalence entre certains porteurs de seaux, qui sont aussi applicateurs d’un jour à l’autre.
Asphalteurs : les outils et équipements du métier
Les outils des porteurs de seaux et applicateurs sont des outils issus de la tradition. Ils n’ont pas connu d’évolutions notables, malgré des tentatives d’amélioration.
Les seaux
Les seaux sont constitués de bois et de métal, tous très semblables d’une entreprise à l’autre, avec une anse en métal. Ils pèsent 5 kg à vide, pour environ 25 kg pleins et une contenance de 10 litres. Des modifications marginales ont été apportées en lien avec le fabricant (forme et attaches de l’anse). Les expérimentations de contenants plus légers n’ont pas apporté satisfaction aux utilisateurs, en termes de maintien en température, de résistance aux sollicitations, au produit, de « nettoyabilité »…
En fin de journée, les seaux utilisés sont mis à tremper, a minima une nuit et plus souvent plusieurs jours, dans une solution d’eau et, si nécessaire, d’un produit débituminant. L’asphalte s’écoule d’autant mieux que le seau est propre et humide. Ils sont donc plus faciles à vider en début de journée.
Les palettes des applicateurs
Toujours en bois, elles peuvent différer par leurs dimensions, leur forme et le type de poignée.
Les opérateurs observés portent des équipements de protection individuelle (EPI) : casque, gants, chaussures de sécurité, vêtements de travail haute visibilité pour tous et des genouillères pour les applicateurs. Les gants, chaussures et vêtements sont adaptés à la chaleur de l’asphalte.
Un camion malaxeur transporte l’asphalte et assure son maintien en température. Ce camion est équipé d’une sortie arrière avec goulotte. Il est également doté d’un réservoir d’eau.
Dans certaines situations où l’accès est impossible à un poids lourd, un « mini-malaxeur », monté sur un motobasculeur peut être utilisé.
La contrainte du court délai avant que le mélange ne devienne trop visqueux pour être appliqué a un impact sur les temps de trajet entre malaxeur et lieu d’application ainsi que sur les éventuelles solutions de mécanisation de l’acheminement.
Quels sont les facteurs de risques de TMS liés à l’activité des porteurs de seaux ?
Les facteurs de risques de troubles musculosquelettiques sont principalement liés aux manutentions manuelles et aux postures sollicitantes pour les porteurs de seaux. Ils seront différents selon les phases de leur activité :
Remplissage des seaux | Transport des seaux (vides/pleins) | Dépose de l'asphalte auprès de l'applicateur |
- Manutentions du seau à hauteur de goulotte | - Port de charge avec déplacement | - Posture en flexion du tronc avec charge |
- Prise et dépose des seaux sur la plateforme de remplissage | - Postures en déséquilibre | - Manipulations du seau plein |
- Prise et dépose des seaux au sol |
Leurs autres contributions à l’activité du collectif peuvent également être sources de contraintes : lors de l’aspersion d’eau après application (pour accélérer le refroidissement de l’asphalte avant de rendre l’espace à la circulation piétonne), de la manipulation des éléments de signalisation temporaire, de la manutention des moules métalliques pour la finition quadrillée…
Une analyse quantitative détaillée de l’activité a été réalisée lors de plusieurs séquences de travail sur deux chantiers de configurations différentes : l’un avec une distance courte (< à 5 m) entre le camion malaxeur et la zone d’application de l’asphalte ; l’autre avec une distance plus longue (> à 10 m). Ces données ont permis de construire des chroniques de l’activité des porteurs de seaux portant sur des séquences de même ordre de durée (7 mn et 4’40).
L’analyse de l’activité d’un porteur de seaux montre ici que la courte distance (moins de 5 m) entre le camion et l’applicateur rend les cycles de travail (remplissage/transport/dépose/retour) plus rapides (25 secondes en moyenne) et plus rapprochés (10 cycles en 7 mn). Les temps d’attente, avant le remplissage ou auprès de l’applicateur, en attente de ses consignes pour la dépose, sont significatifs, ils représentent 31 % du temps de travail sur la séquence.
La manutention manuelle des seaux représente 60 % du temps d’observation sur cette séquence, dont plus de la moitié lors des déplacements avec le seau vide et lors des temps d’attente. Par ailleurs, sur cette observation le temps passé en position statique était prédominant par rapport au temps de déplacement (deux tiers/un tiers).
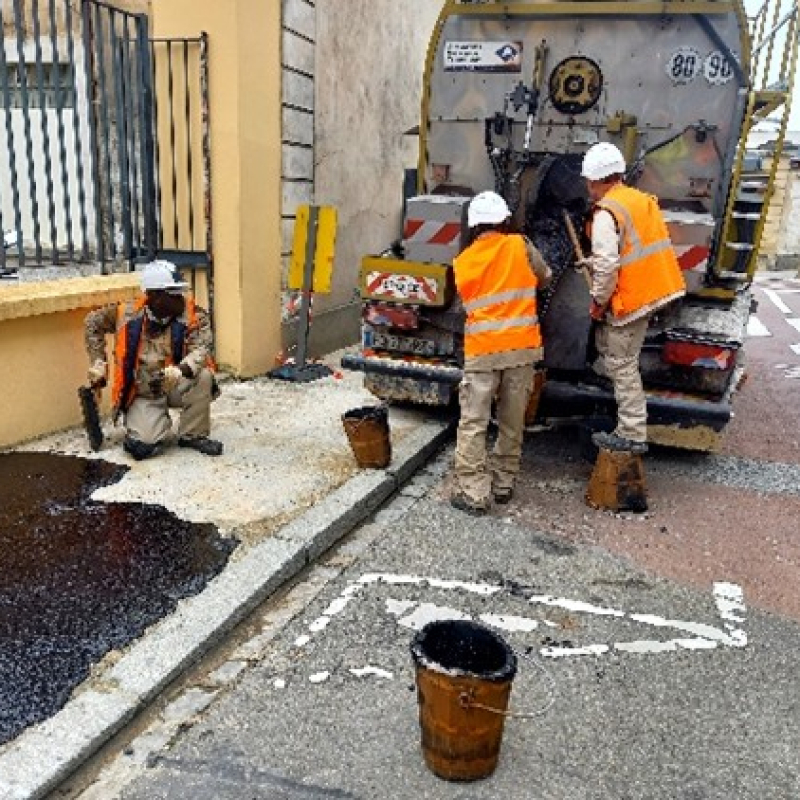
Remplissage des seaux : distance entre le camion et l'applicateur
En termes de postures de travail, l’opérateur a principalement le tronc en position verticale ; la flexion du dos représente 7 % du temps. Elle est systématiquement associée à la dépose d’asphalte.
Chronique de l’activité sur chantier 2 (4’40) : distance plus longue entre camion et applicateur
Lorsque la distance augmente (ici supérieure à 10 m), la durée des cycles (55 secondes en moyenne) augmente et leur fréquence (4 en 4’40) se réduit naturellement pour chaque porteur de seaux. La proportion du temps passé en manutention d’un seau (vide ou plein) est semblable au cas précédent, il inclut des temps d’attente restant significatifs, mais qui se réduisent en pourcentage du temps total (22 %) mais pas en durée unitaire.
On retrouve pour chaque déplacement une distance plus grande à parcourir et un peu moins de temps de récupération.
À l’inverse du cas précédent, le temps passé en déplacement est un peu supérieur au temps passé en statique (53 % vs 47 %) sur le total de temps de manutention.
Les observations concernant les postures sont semblables à la situation précédente (flexion du tronc lors de la dépose).
Les risques de TMS lors du remplissage des seaux
Le porteur amène le seau vide sous la goulotte du camion malaxeur. Le seau est alors posé sur une plateforme prévue à cet effet.
Sur les chantiers observés, le remplissage dure en moyenne 15 secondes avec une durée variant entre 6 et 30 secondes (cf. chroniques d’activité ci-dessus), mais souvent inférieure à 10 secondes. Les seaux sont remplis au maximum de leur capacité.
La vitesse d’écoulement de l’asphalte varie au cours du temps (température, dépôts sur la goulotte…) ; elle peut être réglée grâce à une commande hydraulique disposée sur le côté de la goulotte qui ouvre, plus ou moins le dispositif de sortie de l’asphalte.
Lorsque l’asphalte durcit dans la goulotte, les opérateurs grattent la goulotte avec une spatule pour maintenir la fluidité de l’écoulement ; de même lorsque celui-ci ralentit, on voit les porteurs de seaux utiliser le fond du seau qu’ils vont remplir pour racler la goulotte, afin d’augmenter le flux d’asphalte pour le remplissage du seau précédent.
Afin de ne pas arrêter l’écoulement de l’asphalte dans la goulotte, les porteurs de seaux se relaient : avant même que le premier seau soit totalement rempli, le second porteur de seau positionne son seau au niveau de la goulotte pour prendre le relais dès que le seau précédent est plein, juste avant qu’il soit retiré du plateau par son collègue. Dans cette action, l’opérateur doit maintenir le seau en hauteur un bref instant, à chaque remplissage. Ce maintien ne dure que 2 ou 3 secondes. Il s’effectue bras tendus, position sollicitant les épaules et le dos, par le porte-à-faux ainsi généré.
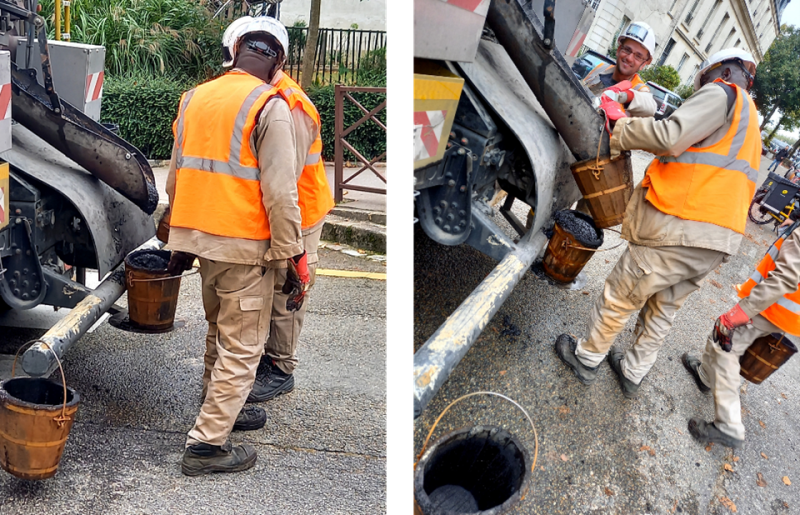
Relais de porteurs de seaux après écoulement de l'asphalte
La cadence de l’opération est donc déterminée par le temps de remplissage d’un seau et le nombre de porteurs. Si la distance au lieu d’application risque de ne pas permettre au porteur de faire l’aller-retour dans le temps de remplissage du seau suivant, le nombre de porteurs prévus sera augmenté.
En termes de postures de travail, les porteurs de seaux se tiennent principalement le « dos droit » lors du remplissage. Les flexions du tronc sont de courtes durées, pour la mise en place et le retrait du seau sur le plateau ou la prise ou dépose au sol en attendant que le porteur précédent laisse la place.
Lors des observations, le réglage a été modifié de 30 cm à 45 cm du sol, pour amener l’anse du seau proche de la hauteur du bassin (selon la taille des opérateurs). C’est au moment de la prise (seau plein) sur la plateforme que l’effort peut être le plus sollicitant, surtout pour le membre supérieur. Cependant, cet effort sera réduit si la hauteur de la plateforme est adaptée aux caractéristiques de l’opérateur, pour lui permettre de n’avoir ni à soulever ni à retenir la descente du seau à sa prise).
Pour autant, les salariés et leur encadrement reconnaissent n’utiliser que rarement ce réglage de la hauteur, même perçu comme inadéquat.
Dans cette phase de l’activité, c’est donc la répétition des efforts liés aux manutentions de seaux, et en particulier des seaux pleins, qui est sollicitante, plus que les postures statiques de travail.
Les déterminants de l’activité physique à cette phase sont :
La coordination entre les porteurs de seaux pour la régularité de l’écoulement de l’asphalte et de l’approvisionnement des applicateurs ;
La hauteur de la plateforme de dépose du seau (et la possibilité technique offerte par le matériel d’en ajuster la hauteur aux opérateurs) ;
Les caractéristiques (instantanées) de l’asphalte, plus ou moins fluide à l’écoulement ;
Les caractéristiques de la goulotte (sa largeur, variable selon les camions, sa résistance à l’écoulement, etc.).
Les observations ont montré que le temps d’attente au remplissage des seaux en asphalte peut représenter une durée significative (entre 22 % et 31 % du temps sur les chantiers analysés), permettant des micro-pauses, protectrices face aux contraintes physiques auxquelles les porteurs sont exposés ici.
Les risques de TMS lors du transport des seaux
L’opérateur porte les seaux pleins d’asphalte du camion malaxeur à l’applicateur. La manutention est réalisée sans matériel, sur une distance qui peut varier de quelques mètres jusqu’à, plus rarement, plusieurs centaines de mètres. Sur les chantiers observés, les distances variaient de 3 à 25 m en fonction de l’avancement du chantier.
Si la durée du déplacement du porteur avec son seau est trop importante (grande distance, obstacles, escaliers…) pour permettre un approvisionnement de l’applicateur avec un asphalte à température convenable, d’autres solutions seront envisagées (équipements supplémentaires).
Le seau est plein à l’aller (poids environ 25 kg) et vide au retour (poids environ 5 kg). Les seaux vides tendent à s’alourdir avec le temps, lorsque de l’asphalte reste collé au fond.
L’objectif du porteur est d’approvisionner l’applicateur de façon la plus régulière possible, en s’adaptant au rythme de travail de celui-ci. Le porteur lui permet ainsi de maintenir une activité sans interruption et optimise le temps du chantier.
Le plus souvent, les porteurs de seaux acheminent les seaux un par un, avec un côté préférentiel (main dominante). Il arrive qu’ils portent deux seaux en même temps (50 kg), un dans chaque main, pour limiter les allers-retours entre le camion et la zone d’application lorsque la distance augmente, cependant cette pratique est peu fréquente. Le gain lié à l’équilibration des charges, portées symétriquement, ne compense pas la charge physique liée au poids des deux seaux.
Dans les chantiers observés, la distance de déplacement est en moyenne inférieure à 5 m, le camion manœuvrant pour se déplacer avec l’avancement du chantier. Cependant, dans certaines situations, le camion est contraint de rester à distance (> à 10 m) de la zone d’application.
« Le plus difficile avec les seaux, c’est la distance », disent spontanément les porteurs. Ils sont parfois contraints dans leur parcours, en ayant dans certains cas à contourner des obstacles (véhicules, mobilier urbain…) qui peuvent empêcher les opérateurs à maintenir l’équilibre corporel trouvé dans la manutention des seaux pleins et majorer les contraintes physiques.
À cette étape, ce sont donc de nouveau les manutentions qui sont le principal facteur de risque de TMS, par les poids manutentionnés, unitairement et de façon cumulée, les distances à parcourir « en charge » et le rythme à maintenir, réduisant les marges de manœuvre des porteurs.
Pour autant, les postures de travail constituent également un facteur de risque significatif, du fait du déséquilibre lié au port unilatéral et à la nécessité de ramener le centre de gravité à la verticale des appuis, via une inclinaison latérale du tronc et un écartement du bras opposé au seau.
L’option de porter deux seaux à moitié remplis pour permettre une sollicitation symétrique, tout en restant sur des niveaux de charges proches de ceux définis dans les normes (NF X35-109), n’est pas considérée comme envisageable par les porteurs (perte de temps, multiplication des déposes et remplissages).
Même avec des gants épais, l’anse du seau rend la prise inconfortable, compte tenu de son diamètre inférieur à 1 cm, en particulier lorsque la distance augmente. L’entreprise a travaillé avec le fournisseur pour améliorer l’attache de l’anse sur le seau. Des tentatives d’élargissement de l’anse pour améliorer le confort de la prise ont également été réalisées, mais ne se sont pas révélées satisfaisantes jusqu’ici.
Les déterminants de l’activité physique à cette phase sont :
Les caractéristiques du chantier : la distance de déplacement entre le camion et l’applicateur, la continuité de cheminement (obstacles, escaliers…) ;
Les caractéristiques des seaux (poids, forme de l’anse qui détermine le type de prise) ;
La coordination avec les applicateurs pour permettre la régularité du cheminement, sans temps d’attente en charge ni précipitation.
Deux types de chantiers ont été observés :
un « gros » chantier où la totalité de la journée se déroule sur un même lieu, où la superficie à asphalter est importante (et la quantité d’asphalte à appliquer est proche de la quantité d’asphalte embarquée dans le malaxeur) ;
une journée faite de l’enchaînement de « petits » chantiers de superficies à traiter plus restreintes.
Les observations montrent que la contrainte varie également selon le type de chantier en lien avec le nombre de répétitions et les temps de récupération :
Lorsque la superficie à couvrir est importante, le nombre de cycles enchaînés en continu est plus conséquent, « quand on enchaîne, c’est plus dur physiquement » ;
L’enchaînement des cycles de manière discontinue (enchaînement de plusieurs petits chantiers sur des lieux d’intervention différents et de surfaces à couvrir plus réduites) est ressenti comme « moins physique ». Il y a davantage de temps d’attente, de récupération (facteur protecteur sur le plan physique), même si la baisse ressentie d’activité n’est pas toujours psychologiquement bien vécue par les opérateurs.
Lors des observations réalisées, la part de l’activité dévolue à la manutention manuelle représente entre 50 % et 60 % du temps (quelle que soit la distance), dont plus de la moitié en déplacement, avec des seaux vides d’asphalte et sur du temps d’attente.
Sur un des chantiers mobilisant quatre compagnons porteurs de seaux, sur des distances de transport majoritairement courtes, l’observation de l’activité sur 5 h 15 (sur plusieurs chantiers successifs, dont 1 h 10 de pause et attente de la fin d’une averse) a permis de dénombrer 180 seaux portés en moyenne par compagnon (de 176 à 235 selon les opérateurs) avec un temps moyen de transport de 7 secondes. Cela correspond à près de 5 tonnes manipulées par opérateur. Mais plus encore que le poids total cumulé sur la journée, le facteur principal de risque est plutôt l’enchaînement rapide de manutentions – avec déplacements – de charges d’un poids significatif et d’un confort de préhension médiocre.
Les risques de TMS lors de la dépose de l'asphalte auprès de l'applicateur
Le porteur dépose l’asphalte à côté des applicateurs. Plusieurs techniques sont utilisées, selon les compagnons, la qualité du seau et la viscosité de l’asphalte. On voit certains porteurs « lancer l’asphalte » et d’autres (ou les mêmes opérateurs à d’autres moments) « frapper le seau au sol ». Dans les deux cas, l’action est très rapide et amène le porteur à soulever le seau et se pencher pour saisir le bord du fond du seau avec une main, l’autre restant à tenir l’anse.
La coopération entre le porteur et l’applicateur est déterminante pour l’activité de chacun et pour la qualité du résultat. L’objectif du porteur de seau est de déposer l’asphalte à proximité immédiate des applicateurs, pour permettre à ceux-ci de l’appliquer de manière continue et à moindre coût physique. Une dépose de l’asphalte au plus près de la zone à recouvrir évitera des efforts inutiles et une perte du temps à l’applicateur.
Les deux techniques de dépose les plus fréquentes ont été retrouvées régulièrement sur les chantiers observés. La technique de « lancer l’asphalte » permet d’éviter de se baisser mais il est nécessaire de viser juste à proximité de l’applicateur sans le toucher. La technique consistant à « frapper le seau au sol », nécessite de se baisser davantage sur la zone que l’on vise. Elle est souvent préférée dès lors que l’asphalte colle aux seaux.
Dans les deux cas, les compagnons utilisent une main pour tenir l’anse et l’autre pour basculer le seau, en tenant le rebord extérieur du fond du seau. Les deux techniques demandent un effort pour porter le seau et pour lancer l’asphalte ou frapper le seau au sol. Ces gestes sont réalisés sur quelques secondes.
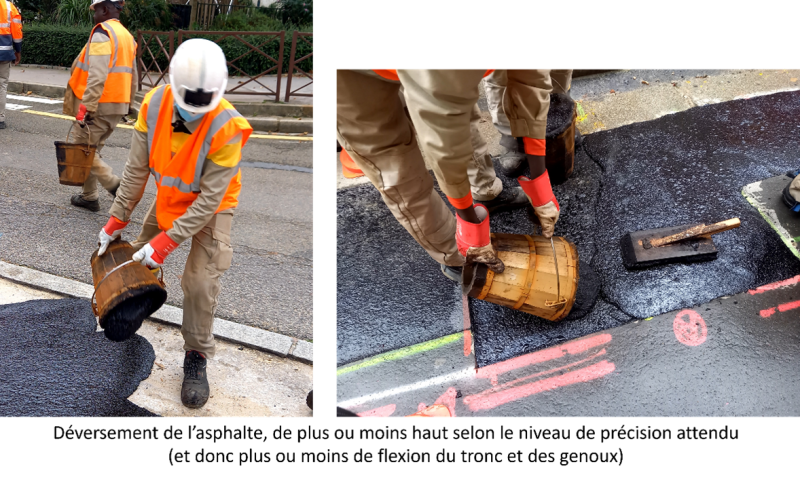
Les seaux sont le plus souvent vidés entièrement, en une fois, et plus ponctuellement en partie selon les besoins des applicateurs. Très occasionnellement, les compagnons peuvent réaliser un ajustement de niveau avec l’asphalte (sol avec pente ou raccord). Ils déposent alors l’asphalte au fur et à mesure en retournant le seau et en le « traînant » au sol (cf. photo). Compte tenu du déplacement à associer, l’action est réalisée en général avec le dos en grande flexion et les genoux tendus.
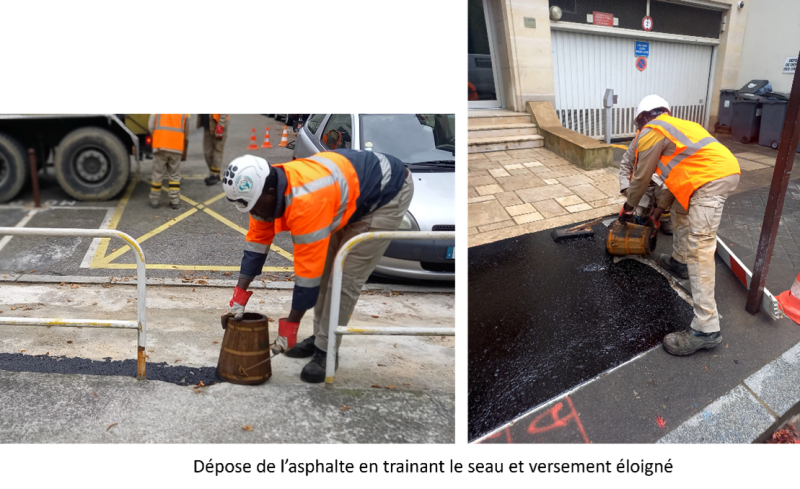
Il arrive également que le seau d’asphalte ait à être déversé sur un point moins accessible pour le porteur, l’obligeant à des postures contraignantes (avec seau plein) notamment en torsion du tronc ou éloigné, bras tendus et dos fléchi, en porte-à-faux (cf. photo).
Les déterminants des contraintes physiques à cette étape sont :
Les caractéristiques des seaux (poids, forme et diamètre de l’anse du seau (prise fine), adhérence de l’asphalte au seau) ;
Les modes opératoires et techniques gestuelles associées.
Les facteurs aggravants
Compte tenu du caractère multifactoriel du risque de TMS, différents facteurs peuvent être considérés selon les situations, comme susceptibles de diminuer ou d’aggraver, directement ou non, l’exposition au risque de TMS.
En lien avec le matériau travaillé : la qualité et la température de l’asphalte ;
En lien avec les contraintes organisationnelles (exigences du client, contraintes liées à l’environnement…) :
En fonction des délais de réalisation des chantiers à respecter mais pas toujours bien calibrés ;
Selon les contraintes d’horaires (imposées ou à éviter, trafic auto – piéton, accès aux commerces…).
Des compromis, potentiellement sources de contraintes, peuvent être mis en œuvre par exemple face aux risques de ne pas réaliser le chantier dans les temps et d’avoir à revenir ; ou de rencontrer des difficultés dans l’optimisation des enchaînements de chantiers (selon les exigences de chaque client) ; ou encore dans le choix des moyens techniques et humains à mettre à disposition, pour aider dans le transfert des seaux du camion à la zone d’application, selon l’accessibilité des chantiers (augmentation des contraintes physiques)…
1. En lien avec l’environnement de chantier :
Gestion des usagers (piétons, véhicules) : interrompre son activité, les réorienter, les faire patienter, gérer les conflits…
La météo : renoncer à démarrer le chantier, ou devoir en accélérer l’exécution sous la menace d’une dégradation des conditions météo, devoir arrêter le chantier en cours.
2. En lien avec l’organisation du travail mise en place par l’entreprise et la qualité des coordinations :
Les ressources disponibles sur le chantier (nombre de compagnons, expériences et compétences, polyvalence…) ;
La synchronisation des rythmes de travail dans la coordination au sein de l’équipe : chauffeur – équipe d’asphalteurs (avancement du camion, protection…), porteurs – applicateurs et porteurs entre eux ;
L’anticipation et la coordination avec les clients (et autorités publiques pour l’emprise sur la voirie ou blocage de circulation) et les usagers (commerces, riverains) le jour du chantier et en amont.
Les autres risques
L’activité des porteurs de seaux d’asphalte peut exposer ceux-ci à d’autres risques que ceux liés à leur activité physique. Ces autres risques n’étaient pas directement ciblés par l’étude présentée dans ce document, ils ne seront donc pas développés ici. Ils doivent cependant rester présents à l’esprit de tous dans le cadre de l’approche globale de la prévention et comme facteurs potentiellement aggravants des risques de TMS.
Sans faire une évaluation exhaustive des risques, on relève notamment :
Les risques liés aux émissions de fumées et de vapeurs : l'asphalte chaud émet des fumées et des vapeurs qui peuvent contenir des hydrocarbures aromatiques polycycliques (HAP), des composés organiques volatils et autres substances chimiques ;
Les risques de contacts cutanés pouvant entraîner des irritations ou des brûlures en raison de la température élevée de l'asphalte ;
Les risques liés au travail sur voie circulée (risque de heurts, de troubles psychosociaux) ;
Les risques de troubles psychosociaux du fait des relations avec les usagers de la voirie (piétons, automobilistes), voire violences externes.
Les préconisations
Des pistes d’améliorations sont déjà mises en œuvre dans certaines entreprises ou certaines situations, l’objectif étant de chercher à systématiser ou à généraliser ces pratiques de prévention.
Sur le matériau
Une température maximale de fabrication, transport et application de l’asphalte coulé réduite à moins de 200 °C (sans augmentation des contraintes liées à son application) ;
Maintien d'une température de sortie la plus constante possible pendant toute la durée du chantier.
Sur l’organisation du travail
Un ratio minimal systématiquement prescrit de deux porteurs de seaux pour un applicateur ;
Un renfort de porteurs de seaux dès lors que les distances sont importantes entre le camion et la zone d’application ;
Coordination entre le chauffeur, le porteur de seaux et l’applicateur : souplesse d’ajustement de la vitesse de remplissage des seaux selon le rythme d’application (manette au niveau de la sortie de goulotte), avancement du camion au fur et à mesure de l’application, dépose de l’asphalte à proximité de l’applicateur ;
Renforcer la coordination entre les porteurs de seaux et les applicateurs : gestion des temps d’attente (= temps de récupération) ; « ne pas porter les seaux » à vide pendant les temps d’attente ;
Se doter des moyens d’une régulation réactive et efficace en gestion des effectifs face aux aléas en lien (ex : absences).
Sur la planification
Trempage des seaux en bois au préalable de leur utilisation pendant 48 heures au moins (« éviter que l’asphalte ne colle au fond du seau ») ;
Décision de la fabrication de l’asphalte en dernière minute pour ne pas risquer de perdre l’asphalte (aléas équipement, aléas météo, etc.) ;
Optimisation des déplacements : regroupement des chantiers à réaliser sur une même commune ;
Surveiller l’enchaînement des chantiers, rechercher l’alternance entre « gros » et « petits » chantiers), y compris dans les reports issus d’aléas sur des chantiers.
Coordination avec les acteurs externes :
Identifier les impacts sur les conditions de travail des décisions issues de la coordination avec les clients (gestion des délais chantier, plus ou moins serrés) et renforcer la coordination en amont (accès au chantier, préparation de l’aménagement du chantier…) avec les interlocuteurs concernés par la voirie (police, services techniques, commerces…).
Sur les outils de travail
Organiser un suivi rigoureux concernant la gestion des seaux en bois : trempage en amont de l'activité (donc disposer d’un parc important), inspection (usure, déformation…) après trempage et avant remise en circuit (donc disposer d’un stock tampon de seaux neufs), possibilité aux porteurs de seaux de signaler et mettre à l’écart les seaux abîmés ; suivi de l’entretien du matériel de manière générale ;
Ajustement ou modification des anneaux d’accroche des anses sur les seaux pour éviter les accroches avec les porteurs de seaux dans leur activité ;
Utilisation de chariots pour transporter les seaux, afin d’éviter ou de limiter les manutentions manuelles entre le camion et la zone d’application, dès que la distance augmente.
Sur les moyens
État des lieux sur les essais menés sur les équipements d’aide à la manutention existants dans la branche pour identifier les marges de manœuvre (freins rencontrés, bonnes pratiques), pour réduire la distance manutentionnée avec les seaux et/ou améliorer les conditions de manutention lors du transport ;
Explorer les possibilités de mécanisation de la mise à disposition de l’asphalte aux applicateurs :
Avec des systèmes techniques reliés au camion (bras articulé, avec vis sans fin, maintien en température, nettoyable) comparables à ceux développés pour les enrobés (ex : Theam) ;
Avec des équipements motorisés d’aide à la manutention permettant d’approvisionner des lieux d’application éloignés ou difficiles d’accès : contenant isolé/chauffant, sur roues ou chenilles (escaliers) avec goulotte.
Veiller à l’adéquation à l’activité des caractéristiques des camions malaxeurs et de leur équipement : type de goulotte, hauteur plateau, manette de réglage, dispositif de maintien en température de l’asphalte et de réglage ;
Questionner les fournisseurs sur les évolutions possibles des seaux en bois : caractéristiques de l’anse et de ses attaches, poids, adhérence.
Sur les EPI
Maintenir une veille sur les EPI les plus confortables et efficaces, avec une protection efficace contre la chaleur, tout en préservant la dextérité.